What is Porosity in Welding: Vital Tips for Getting Flawless Welds
Porosity in Welding: Identifying Common Issues and Implementing Finest Practices for Avoidance
Porosity in welding is a prevalent issue that usually goes undetected till it triggers considerable problems with the integrity of welds. This common flaw can endanger the toughness and sturdiness of welded frameworks, posturing security threats and leading to expensive rework. By recognizing the origin of porosity and applying effective avoidance approaches, welders can considerably boost the top quality and reliability of their welds. In this conversation, we will discover the essential elements adding to porosity formation, analyze its damaging impacts on weld efficiency, and go over the most effective methods that can be embraced to lessen porosity incident in welding processes.
Usual Reasons of Porosity

Another regular wrongdoer behind porosity is the existence of pollutants externally of the base metal, such as oil, oil, or corrosion. When these pollutants are not successfully removed before welding, they can vaporize and become trapped in the weld, causing issues. Furthermore, using filthy or damp filler materials can present contaminations into the weld, adding to porosity concerns. To alleviate these usual reasons for porosity, thorough cleaning of base metals, appropriate shielding gas option, and adherence to ideal welding specifications are vital practices in achieving top quality, porosity-free welds.
Impact of Porosity on Weld Quality

The existence of porosity in welding can considerably compromise the architectural integrity and mechanical properties of bonded joints. Porosity creates spaces within the weld steel, weakening its general stamina and load-bearing capability. These voids function as anxiety concentration factors, making the weld more vulnerable to splitting and failing under applied loads. Additionally, porosity can lower the weld's resistance to deterioration and other ecological aspects, better decreasing its durability and efficiency.
One of the primary effects of porosity is a decrease in the weld's ductility and durability. Welds with high porosity degrees often tend to display lower influence stamina and reduced ability to deform plastically prior to fracturing. This can be particularly worrying in applications where the welded elements are subjected to dynamic or cyclic loading conditions. Porosity can hinder the weld's capability to effectively transmit forces, leading to early weld failing and potential safety risks in crucial frameworks. What is Porosity.
Best Practices for Porosity Prevention
To enhance the structural honesty and quality of bonded joints, what certain procedures can be implemented to lessen the incident of porosity throughout the welding procedure? Porosity prevention in welding is crucial to make certain the stability and strength of the final weld. One effective technique is appropriate cleaning of the base steel, eliminating any kind of contaminants such as corrosion, oil, paint, or dampness that might lead to gas entrapment. Ensuring that the welding tools is in excellent condition, with clean consumables and ideal gas flow rates, can also substantially lower porosity. In addition, keeping a secure arc and controlling the welding parameters, such as voltage, current, and travel speed, aids produce a constant weld pool that lessens the risk of gas entrapment. Making use of the appropriate welding technique for the details product being welded, such as adjusting the welding angle and gun placement, can better stop porosity. Regular evaluation of welds and instant removal of any concerns recognized during the welding procedure are necessary techniques More Info to stop porosity and produce high-grade welds.
Relevance of Appropriate Welding Strategies
Applying appropriate welding strategies is critical in making certain the architectural integrity and high quality of welded joints, building upon the foundation of efficient porosity avoidance procedures. Too much warmth can lead to enhanced porosity due to the entrapment of gases in the weld swimming pool. Furthermore, using the appropriate welding specifications, such as voltage, existing, and take a trip rate, is critical for accomplishing audio welds with very little porosity.
Additionally, the option of welding process, whether it be MIG, TIG, or stick welding, must align with the specific demands of the project to guarantee optimal results. Correct cleaning and preparation of the base metal, along with choosing the ideal filler product, are likewise important parts of competent welding techniques. By sticking to these best practices, welders can reduce the Website risk of porosity formation and generate premium, structurally audio welds.
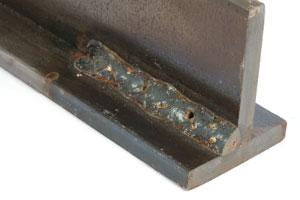
Examining and Quality Assurance Actions
Quality assurance procedures play a vital this website duty in validating the stability and dependability of welded joints. Examining procedures are important to discover and prevent porosity in welding, making certain the stamina and sturdiness of the final item. Non-destructive testing methods such as ultrasonic testing, radiographic screening, and aesthetic examination are commonly utilized to identify prospective issues like porosity. These strategies allow for the assessment of weld quality without endangering the integrity of the joint. What is Porosity.
Post-weld evaluations, on the other hand, evaluate the final weld for any defects, including porosity, and verify that it satisfies defined criteria. Applying a thorough high quality control strategy that includes detailed screening procedures and assessments is paramount to decreasing porosity issues and making certain the general quality of welded joints.
Conclusion
In conclusion, porosity in welding can be a common issue that impacts the high quality of welds. By recognizing the common root causes of porosity and applying finest techniques for prevention, such as proper welding techniques and screening measures, welders can ensure top quality and trusted welds. It is necessary to prioritize prevention approaches to lessen the occurrence of porosity and keep the stability of bonded structures.